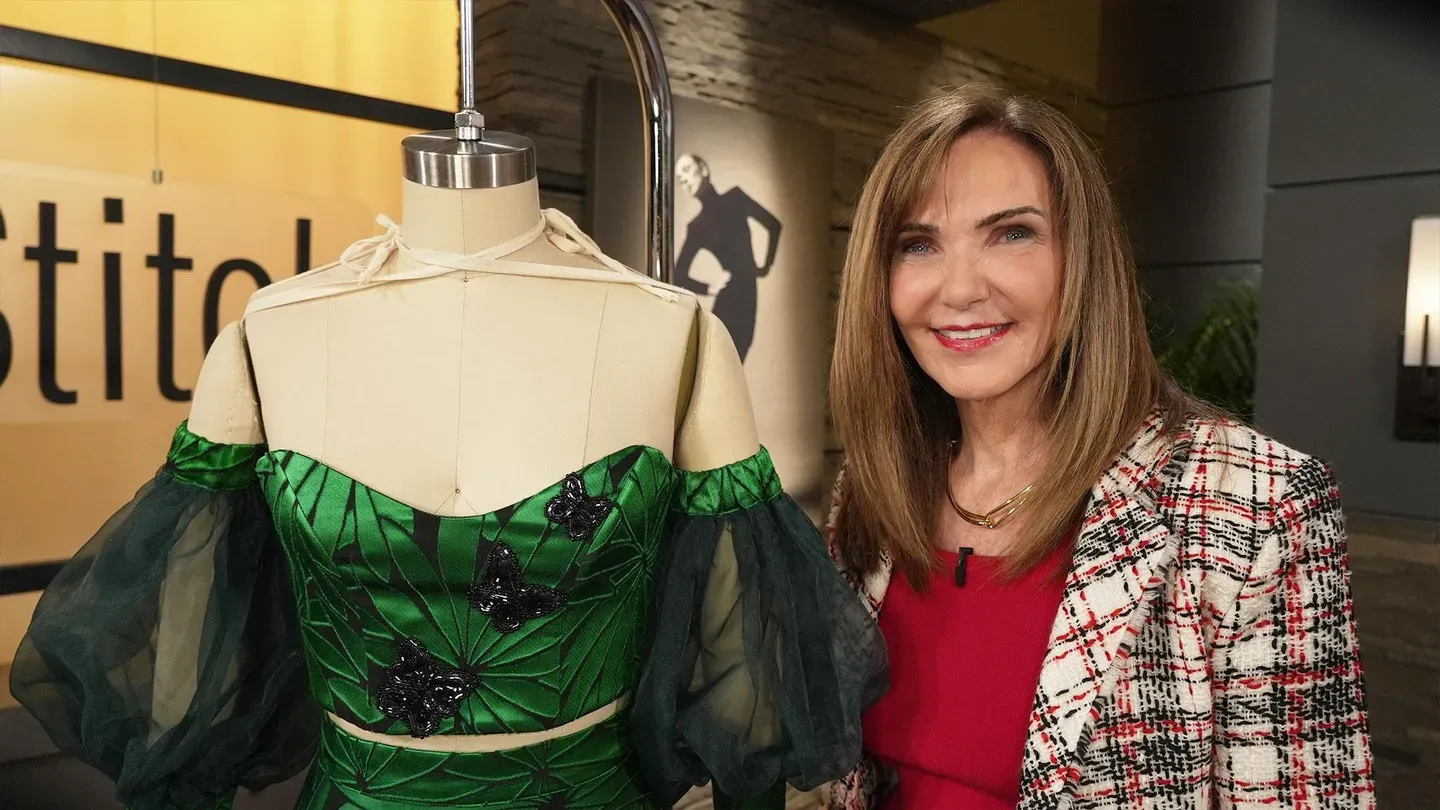
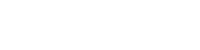
#1104
Season 11 Episode 1104 | 26m 45sVideo has Closed Captions
Peggy Sagers looks at how top designers use interfacing and for what purpose.
Why use interfacing in our garments? Host Peggy Sagers looks at how top designers use interfacing and for what purpose. She demonstrates the basics of selecting and applying fusing materials to your fabrics.
Problems with Closed Captions? Closed Captioning Feedback
Problems with Closed Captions? Closed Captioning Feedback
Fit 2 Stitch is presented by your local public television station.
Distributed nationally by American Public Television
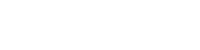
#1104
Season 11 Episode 1104 | 26m 45sVideo has Closed Captions
Why use interfacing in our garments? Host Peggy Sagers looks at how top designers use interfacing and for what purpose. She demonstrates the basics of selecting and applying fusing materials to your fabrics.
Problems with Closed Captions? Closed Captioning Feedback
How to Watch Fit 2 Stitch
Fit 2 Stitch is available to stream on pbs.org and the free PBS App, available on iPhone, Apple TV, Android TV, Android smartphones, Amazon Fire TV, Amazon Fire Tablet, Roku, Samsung Smart TV, and Vizio.
Providing Support for PBS.org
Learn Moreabout PBS online sponsorshipPeggy Sagers: Coco Chanel always said that the inside of a garment ought to be as beautiful as the outside.
What are the most current trends and what should we be using inside our garments to make them look professional?
Today we discuss the most common uses for interfacing, fusible interfacing, elastics, and more.
Join us as we become the best spies on the planet and uncover those secrets from several sources inside the garment industry with over 100 cumulative years of experience.
♪♪ ♪♪ announcer: "Fit 2 Stitch" is made possible by Kai Scissors.
♪♪ announcer: Plano Sewing Center.
♪♪ announcer: Elliott Berman Textiles.
♪♪ announcer: Bennos Buttons.
♪♪ announcer: Imitation of Life.
♪♪ announcer: And Clutch Nails.
♪♪ Peggy: Today we're just gonna play.
We're gonna play with zippers and interfacings and elastics and we're just gonna root--just bare some truths about all of those things.
I have several sources that I purchase items from, wholesale sources, and combined, the gentlemen and the women that I spoke with, over 100 years of experience in these areas, so I feel so certain of the details and I'm just so excited to share them with you, because I think there's so much controversy sometimes about some very simple things that we just don't need to be arguing about.
However, the common theme among all of this was that it's the designer's choice.
It's the designer's choice.
So, I'm gonna default to you many times because it's the designer's choice and sometimes we get frustrated of that because we just want somebody to tell us what to do, which one to use or where to go.
And sometimes that designer's choice can almost feel a little bit overwhelming.
But there are times I'm going to say, "It's designer's choice."
But let's start with zippers here for just a minute.
So, zippers--I'm gonna start with the easy stuff, is why I'm starting with zippers.
Zippers we know, there's not a lot of variables to.
We do have tape color and, for most of us, that's kind of really where all our concerns are.
As long as it's the right color we say, "Hey, it's good to go."
But there is such a thing as called a molded teeth and that's a plastic.
And so any time it's smashed flat like that, that's when they call a molded teeth and a molded zipper is fairly more pricey than one that's not, and these two both are not.
And then we have the plastic teeth and the metal teeth.
Then we have an open end and a closed end zipper, and then we have teeth size.
And the only thing I really wanna say about this, because it's always your choice, is that the smaller the teeth, generally, the more finer the garment.
So, really fine fabrics take up small teeth, and the reason that is is so that the fabric will be less likely to catch in the teeth because those really fine fabrics, if they have a big, you know, like this is a number 5 teeth, then many times it will catch because the tooth is so open and big, and that fabric will be affected because of that.
So, zippers are just fun.
We've seen exposed zippers, we've seen contrasting zippers, we've seen all kinds of things, and I don't think we need to limit ourselves.
We are the designer and we get to choose.
When we go to elastics, we're putting elastics in a lot of times and there's two types of elastics and those are braided and woven--braided and knitted.
And typically, we don't wanna use a braided elastic and I don't even have a sample here because it's difficult to find, although interestingly, if we go back to where we had all the mask-making, a lot of those masks had braided elastic on them and you know if it did because your ears were sore in, like, five seconds.
It's very rough, stiff elastic.
So, most of what we use in the apparel industry is what we call a knitted elastic.
And the way you can tell is you just hold it up to the light, you strength it out, and that knitted elastic, you can see right through.
The braided elastic, you'll not be able to see through and so just, again, hold it up.
And in ready-to-wear, you wanna use what's called a knitted elastic.
It's softer, it's gentler.
This is a knitted elastic.
I know it's orange because, again, this was used for a mask and this is where, especially for those who, many of us, who had to wear a mask from sun-up to sundown, this was really much softer on us.
So, those elastics, just watch for that knitted elastic, and you don't ever wanna sew through elastic.
You wanna always put it into what's called a channel.
But just keep in mind that when you do a knitted elastic, generally it will have ribs on it, and I can cut right through those ribs and I don't lose any property of the stretch of the elastic at all.
As long as I'm cutting in between the ribs, I can start with a wider elastic and keep it on hand and then cut it to any width that I want.
But when you're inserting it in a garment, you're best not to sew through it.
Typically, even in swimwear, bras, and things like that, when they put elastic in, they'll do a zigzag stitch, but the zigzag goes to both sides of the elastic and it doesn't penetrate the elastic.
If it does, it starts to weaken the elastic and your elastic will not last as long.
So, in your sewing efforts, you wanna look to make either casings or some type of channel where that elastic can go through.
So, now the most fun part to me starts with interfacings.
You know, interesting, the history of interfacings.
Interfacings really play different roles and they took on different roles, and we always see this when manufacturers are trying to get their goods made for less money or get more profit margin or all of those things, because interfacings for--in the '50s and '60s were really used to just kind of poof things up a little bit, as an underlayer.
Interfacings were used as an underlayer.
But then in the '70s what came along is the whole fusible concept, that we could just fuse it to the fabric and that would make it much faster and less expensive.
So, when we talk about interfacings, we talk about the wovens or the non-wovens, the sew-in, and then the fusibles.
So, there's those different categories and we're gonna look at all of 'em and we're gonna have a lot of fun.
But again, the resounding word that I always kept hearing was, "Well, it's up to the designer, and we're only here to get the designer what they want, and it's their choice."
But they did give me tips as to what was the best selling and what moved the most and what was used the most and why it was used.
So, that's kind of what we're gonna have fun talking about today.
All right, so when you're talking about a fusible interfacing, if you look at it, you're either gonna see a small dot or you're gonna see a little bit of glisten, and that's a resin.
It's actually not a glue.
I always thought it's--it was just a glue that kind of, you know, glued onto the fabric.
It's actually a resin and it actually never melts, it just softens until it takes on the fabric and then, once it cools, it fuses to the fabric.
And so if it doesn't fuse, the reasons it doesn't is there's three components that are gonna be used when we go to fuse fusibles onto fabric, and that's gonna be the heat, and then the time, and then the pressure.
Those three things are gonna be needed.
So, you can see, this is a much less flexible interfacing, but it is fusible 'cause you can see that shine and that's the resin on the back side.
And then you see this and you look at both sides and there's no resin or anything so we know this is a sew-in.
Then we have a weft and what we know about a weft is a weft is actually fusible on both sides.
And so remember that what these were created for was our fabrics are always changing and so, because our fabrics are always changing, our interfacings pretty much have to change along with that because different needs and different garments are being made.
Probably the best of the interfacings, if you can call--say there's a Cadillac of interfacings, would be what they call the knit fusible.
And the knit fusible had a--it does have the dots, the resin on one side, and then the other side is smooth.
But this is actually a woven.
It's knitted, but it's called a knitted interfacing but considered in the woven category, and it's a fusible.
So, this is actually the crème of the crème, as far as interfacings go, and it's the most expensive.
But interestingly enough, to manufacturers, it's not the most commonly sold.
The most commonly sold is the Pellon non-woven fusible interfacing.
So, it's not--it's not a woven fabric at all.
It's just literally pushed together and kept that way and then the glue--not the glue, but the resin is added on top of it.
So, I'm gonna try a couple of these and I'm gonna show you what I'm talking about, and this is kind of fun, especially with this weft.
This weft was initially created, again, when I think when we distinguish those differences, it was created as a sewing aid.
It was not supposed to be kind of a fix-all-fix-all, but if you put it between two layers, and then just add your steam, your temperature, and your pressure, and you should always add steam when you're fusing.
Steam is always a positive.
And then always let it cool down.
You can see what it does is it just hems that fabric, and so, again, because it was an aid, the goal was it was supposed to hem temporarily until it was taken to the machine so that if you were doing a curved hem or something that was a little more complex, it would hold it into place until the machine would come back in.
But through the development of not as many people sewing or whatever it is, this actually became an aid for many people who didn't want to hem, and they just literally pressed their garments together.
And you can do that.
It was meant to hold, it was, you know, it's not going to come apart, and so now they see--you see it in different widths and different lengths, and it's called a weft.
And you can actually just fuse a hem up.
You don't have to--you don't have to sew it.
So, I thought that was kind of interesting.
The fusible, I love the fusible.
The fusible--I think that I dream of all my garments having the fusible.
We're gonna talk about this a little bit.
But let me just say that in the industry, always the fusible is cut a little bit smaller than the iron.
Now, in our home sewing industry, that is not as critical because if I get fusible on my iron, I've got cleaners and I can just clean it up.
But I want you to think about those big presses, how large they are, and to clean that up is really a lot of work and it's a lot of time and it's a lot of money.
So, I'm gonna make sure this resin is on the bottom before I start to fuse this together, and this because I'm using a home iron, I wanna give it ten seconds or so.
It doesn't have to be.
Give it a little bit of steam, just let it sit, and then pull away.
And that is--I think the hardest thing whenever you're fusing is to really have the time and patience to do the whole entire garment that way.
They do fuse yardages in the industry because they have the big machines and the big equipment.
They have all that space for it.
But when it comes to home, I think it's much better to cut the pieces out and cut the layers together because then I have a tendency to really be able to control my surface area a little bit better.
So, you can see, now this is a stretch woven fabric and you can see that, because I used a knit interfacing, and that's why the knit interfacing really was created, because fabrics started to stretch, and I--the designers wanted a fabric that would actually stretch and the interfacing would stretch with it.
So, that's why this one is more expensive, and a lot of designers just don't wanna use it because it's too expensive, but I love it, I love it.
And it's gonna be my favorite and you're gonna see that.
So, because I kept hearing this terminology of "It's up to the designers.
The designers can do what they wanted," I kind of decided to take a little deeper look at what is in some of these high-end designers.
What kind of interfacing do they actually use?
And let's see what's inside.
To me, men's clothing is a no-brainer because it's much more structured and we don't get the variety of softness that we get in women's clothes, so I kind of peeked inside just a generic waistband and what I found was this.
It's a non-woven fusible, fairly stiff, because men just want that support at the waistband and they don't really want anything more.
But then I looked inside a men's coat and we see the same thing.
And interestingly enough, it's a dark coat and it doesn't even match, but, you know, hey, I guess it doesn't matter, but this is a non-woven fusible interfacing, so it's put in there at the hem to give it some weight so that it does accordingly what you want it to do, which is exactly what interfacing does.
Remember, it's a sewing aid.
It helps the bottom not get stretched out when the sewers are sewing it, all of those type of things.
So, in my sewing, I think I've always thought there's really three reasons why we use a fusible interfacing.
One of the reasons is if I have a garment and I have a fabric and it's--I start off with a fabric like this which is sheer and it's beautiful, but I really want it to do something that maybe it shouldn't be doing, as I wanna make a jacket.
And because I don't want you to see all the details of the jacket inside, I actually fused the whole entire jacket.
So, with a fusible interfacing, I actually fused the whole thing.
And, again, I would not try to fuse yardage.
I think it's too hard to control in those situations.
I would cut the pieces and cut the fusible interfacing underneath it, cut it as one, and then come back in and fuse those pieces individually.
You can keep 'em straight around the board and you just have a little bit more control when you go to do that.
The other reason I would fuse is if my fabric itself is fairly lightweight or loosely woven, and that way what it does is it will stabilize those fibers together and it will hold them into place.
And the other reason I fuse is if something is just really lightweight, cashmere for example, when I'm trying to use cashmere, and it's so lightweight it doesn't have a lot of drape, but if it's good body, then I wanna give it some more.
And so I'll use that fusible interfacing to do those.
So, we've got creating and changing the fabric, we've got stabilizing or we've got just when we wanna add some more body to it.
So, then again, I decided to go different levels.
Different levels of manufacturers to see inside and see what interfacings that "designer" decided to use.
So, we first went to designers and this is not to diss any designer at all.
This is just, I think, so that we can all see what is it that's inside of these that they have decided and why did they decide to use it and what was their modus of operation?
And I think if we can look at what other people used and why they used it, I think it really helps.
So, this whole entire jacket was fused and, if you look at this kind of closely, what you're gonna see is this is actually a woven fusible interfacing.
So, for whatever reason, they decided this fabric, possibly 'cause it's a little loosely woven, that it would need the whole entire jacket.
So, the whole entire jacket and, like I said, it took me a while to peel these layers apart, and at first you kind of can't tell, but once you get it apart, you can see that that's a woven interfacing but it's still got that resin on the back side.
Remember, it doesn't melt into the fabric.
It simply softens, so that it can adhere while the process of that pressure is taking place.
So, I thought that was really interesting.
So, then I decided to go upscale a little bit more and I decided to go to Armani.
And so, this is, like I said, not to diss anyone 'cause you all know, probably by now, Armani's definitely my favorite.
We went to Armani and opened up the bottom and all these jackets were gifted to me so I didn't have to buy or ruin anything and I can put 'em all back together.
But we looked inside Armani and, again, what's interesting to me is the whole entire jacket is fused, this time with the knit fusible.
So, see, I knew why I liked Armani.
But if you, again, go inside, it's really hard to see that it is.
I had to go to a little section and actually peel away until I could get and separate it to tell whether it was a woven or a fusible.
So, the reason for using that fusible and the knit is that it's structuring the fabric, the jacket itself, and yet it's very soft and very pliable.
And then there's another layer at the bottom, just at the hems, which is very common for the hems to have another layer in there, and that's a woven and that's just to give it a little bit of weight.
So, I was really pleased to see this inside and I was really happy that I can put my Armani jacket back together, knowingly that I love what's inside.
So, then I took one more because you know Chanel is, you know, the name to do it.
So, I went inside Chanel and I decided to look and that was probably my biggest disappointment so far, is that this is a Chanel jacket and, you know, I mean, I don't think you can find a Chanel jacket under $3000 or $4000, and as I peel this away, this is all a non-woven fusible.
So, when we look at this most commonly sold, this--we go back to.
But as I ask my reps, you know, why do they buy that?
And it's--the answer is because it's inexpensive.
It's very effective, but it's inexpensive.
So, that was a little disheartening to see that inside.
And so I actually went to another Chanel.
I thought, "Certainly, it can't be that way with all Chanels.
I'm sure it's just one."
And this is actually a non-woven fusible also.
So, and again, I still don't think it's all Chanels.
I think it's just hit and miss as to what works for the garment, but I guess to see the lower quality of fusible, I was just almost a little bit upset at that.
So, we'll just leave it at that.
I know that what I love about sewing is I can put into my garment what I know is breathable, what works, what is best for that fabric, and because I don't have to consider cost at every level, I really can accomplish the garment and finish the garment with a beautiful ending, and one that feels good for me.
So, this is a front-facing, and this is another way that designers have answered the questions of using high-end fabrics but not using interfacing is they actually will change the pattern.
So, this is my front-facing and what it does is it folds under.
A seam allowance folds under, and then the blouse front is inserted.
And when that happens, what you get is you get one, two, three layers of actual fabric all the way down the blouse front.
And what that does is that supports the buttons and the buttonholes so I know that I've got plenty of substance and I don't need interfacing at all.
And so that, actually changing the pattern and creating your facings and your pieces to substitute, remember that fusible or interfacings are really only a sewing aid, so I don't necessarily need them at all if I don't want to have them.
Then there's a thing called tie interfacing, and ties, of course, always need interfacing because of the way they're tied.
It's not the fabrics that are being used, it's actually to hold the tie itself.
So, in this particular case, I'm gonna use tie interfacing.
I brought it just like that so you can see the tie.
I'm only gonna use a segment of it because what we know about interfacings is interfacings are used at the shoulder of a jacket.
So, I'm gonna use about 20 inches of this, about half of this, and I'm gonna set in a sleeve.
And in this particular case, I used--I fused this because it was a loosely woven fabric and I wanted to stabilize it a little bit more.
So, I'm gonna go to the sewing machine.
I'm gonna show you in this case how we use interfacings to set in a sleeve for a completely different role is what we're doing right now.
So, I'm gonna turn my machine to baste.
And my baste, I'm gonna put at 6.
And not at the bottom of the sleeve because at the bottom of the sleeve, there's no ease.
All my ease goes from notch up and around to notch.
So, I'm gonna come inside to the inside of that sleeve and I'm going to put my tie interfacing and you're gonna stitch right on the stitch line.
Your interfacing should be--your tie interfacing should be about 1 inch wide, and I'm simply gonna pull.
And when you pull, you're gonna just let the machine do its thing.
Just keep the tension, and the goal here when you're doing this is to try to keep the tension consistently the same and to stay right on the seam allowance.
I'm purposely using a contrasting thread because I'm gonna remove this thread and it's much easier to remove if I can see it.
When I get too matchy-matchy, it's really hard to see it.
All right, so I've gone all the way around from notch to notch.
I'm going to tie that off and now what you see is that interfacing now has actually created a sleeve head for me, and it's done all my easing.
So, it's gonna play two roles.
It's gonna do my easing as well as be my sleeve head.
So, when I come to put it into my jacket, all I have to do here is I'm gonna fold the sleeve, I'm gonna pay attention to where that notch is at the top and, typically, it's a fairly same shaped image, and I'm gonna put a pin here at the bottom, and then I'm going to sew it in place.
I'm gonna align it into my jacket and when I sew, remember that I wanna keep my seam allowances at 3/8 because, again, of this concave-convex situation.
But I can align that here at the top.
I can align it at the bottom where my pins are.
The bottom goes to the underarm seam, as you can see.
We're gonna put that inside.
And so, my pin is there.
I'm gonna turn my machine off of baste, and I'm gonna set that sleeve in.
And what you're gonna see is I actually don't have to really pin this that much because all of my easing has taken place.
But what I do wanna do is be careful to line up those seam allowances and I stitch all the way around.
All right, that's what we're gonna do.
Now, the only reason in showing you this and in putting into the machine is that I really wanna show you that I don't have to worry about trying to ease that sleeve in.
The tie interfacing did all the work for me and, as I pull this around, it's just gonna be beautifully done.
And I'm actually only gonna do a little bit of that because I want to show you what it looks like but, not only what it looks like, but what to do with a shoulder pad.
Because when I've got the sleeve, and I've got it in this section here, the shoulder pad is going to go out into, again, another interim that is right there at the edge.
So, this shoulder pad goes right to the edge.
I flip it around, and that tie interfacing actually becomes the sleeve head.
So, wow, all these things that interfacings do for us are just incredible.
Many of us purchase a dress form and don't use its full power.
A dress form is much more than a clothes rack when you use it correctly.
Next time on "Fit 2 Stitch," we'll fit the sheath dress, prepare the form, and share several options so that you can get the full benefit of your dress form.
Join us.
♪♪ ♪♪ ♪♪ ♪♪ announcer: "Fit 2 Stitch" is made possible by Kai Scissors.
♪♪ announcer: Plano Sewing Center.
♪♪ announcer: Elliott Berman Textiles.
♪♪ announcer: Bennos Buttons.
♪♪ announcer: Imitation of Life.
♪♪ announcer: And Clutch Nails.
♪♪ announcer: To order a four-DVD set of "Fit 2 Stitch," series 11, please visit our website at fit2stitch.com.
Support for PBS provided by:
Fit 2 Stitch is presented by your local public television station.
Distributed nationally by American Public Television